GM Paint Shop Strip Out & Demolition
Paint Shop Spray Booth,
Oven and Process Equipment
Work Performed: Strip Out and Demolition of Paint Shops and Process Equipment
Project Description
Process Equipment Demolition
Warren Transmission Plant, Warren, MI – This project consisted of the final clearing of approximately 440,000 square feet of process area located in General Motors Corporation’s Warren Transmission Plant.
Over the years, the plant went through many changes without any prior removals. The United States Navy and the Hudson Motor Car Company constructed the facility in 1941 to manufacture various artillery and shells. The facility was subsequently owned by Westinghouse and Ford Motor Company before it was purchased by the Chevrolet Motor Division of General Motors in 1961. From 1961 to 1974, the facility was used to manufacture automotive parts and artillery shells. From 1974 to July 1980, Chevrolet continued its automotive manufacturing operations. The Hydra-Matic division of General Motors began operations in 1980 and continues to produce transmissions and various other automotive parts.
It was the task of North American Dismantling to finally clear out all the old and redundant systems that had been collected over the years, including electrical, mechanical, fire protection, heating and ventilating, and security systems. No as-built drawings were available to assist North American Dismantling in this endeavor. Several hundreds of hours were spent identifying and labeling the systems to remain and those to be removed.
All abandoned pipes, conduits, and wires were removed from the inside and below the roof truss of the buildings. Conveyors, mezzanines, catwalks, and their supports no longer used were removed completely. All equipment support brackets were removed. Steel brackets and clamps for pipes and conduits were removed from roof trusses and building columns in the identified dismantling area. North
American Dismantling removed all old equipment structural members, u-bolts, and hangers connected to roof trusses in all areas.
Additionally, North American Dismantling removed 45,000 square feet of wood block flooring, 56,000 sf of concrete pavers, and 244,750 sf of non-monolithic concrete (including topcoats, concrete pads, concrete curbs, and equipment foundations). The wood block flooring and brick pavers were removed and disposed of as regulated materials, and the areas below were scarified to receive new concrete topping.
North American Dismantling also removed several hundred feet of 48” round ductwork, which covered an area of approximately 200,000 sf from the existing roof.
North American Dismantling completed the asbestos abatement of pipes, heater units, and HVAC units located in the truss of the buildings.
North American Dismantling also completed the environmental cleaning of all pits, sumps, flooring, and trenches in all areas.
In addition to our original contract work, North American Dismantling was awarded the removal of approximately 12,000 sf of the existing oven from the roof area. The ovens were contaminated with non-friable ACM. In Addition, North American Dismantling received the proper 40 hr training needed to remove the ovens. The roof, roof panels, and side panels of the Elpo Oven were double-wrapped with 6-mil poly and disposed of as ACM. The remainder of the oven was removed as non-hazardous metal and debris. Because of the high flammability of the roof, North American Dismantling, in conjunction with the Plant Fire Marshall, purchased four plasma cutters and trained its employees to complete these operations.
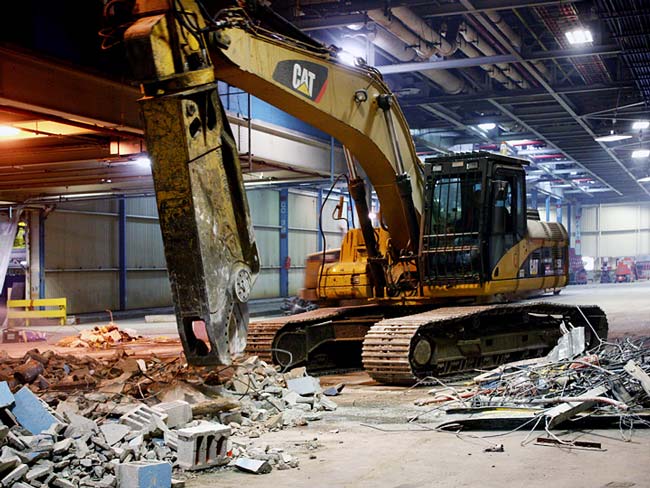
Process Equipment Demolition Paint Shop Spray Booth and Ovens
Moraine, OH – This project consisted of the removal of approximately 50,000 sf of paint ovens and 10,000 sf of paint spray booths located on the second floor and grating level of the plant directly adjacent to the operating paint shop. There were several factors that made this a very complex and unique project. Aside from being located directly adjacent to the paint shop, the second floor and the grating level were built over the old roof (R-1 Level) of the existing assembly plant with an active assembly line located directly below the roof area. The use of water for fire protection had to be minimized and all openings in the R-1 level had to be protected to prevent any foreign mater from entering the assembly area. Also, active paint conveyors were located on the R-1 level directly below the demolition area which had to protected from the demolition operations.</p?
Absolutely no dust or foreign matter could come in contact with these systems. Another hurdle to overcome involved having no major access and egress to the demolition area until NADC designed and installed a series of structural steel bridges consisting of 60 tons of material connecting the demolition areas to a drop zone at the edge of the existing building. This operation required opening the existing building in five separate areas and installing a weather protection system to eliminate any elements from entering the plant. The construction of these bridges included airlifting structural members utilizing helicopters, which was completed on plant down time (Sundays and Holidays). North American Dismantling was also responsible for the design/build of $1,200,000.00 of the structural steel/grating and concrete utilized in filling all openings where the booths and ovens were removed, along with utility disconnects, rerouting and re-supporting and the relocation of existing process equipment. Additionally, during the course of its contract GM requested North American Dismantling remove an existing 240-foot long, 80-foot wide and 80-foot tall Automatic Retrieval System (Stacker Building). This structure was connected on two sides and was 30 foot taller then an existing building, which was to remain. This project was completed on schedule, with limited change orders and without interference to the plant’s existing assembly operations.
Contact us for more detailed information on your industrial strip out project.
Missing Attachment
Paint Shop Spray Booth,
Oven and Process Equipment
Work Performed: Strip Out and Demolition of Paint Shops and Process Equipment
Project Description
Process Equipment Demolition
Warren Transmission Plant, Warren, MI – This project consisted of the final clearing of approximately 440,000 square feet of process area located in General Motors Corporation’s Warren Transmission Plant.
Over the years, the plant went through many changes without any prior removals. The United States Navy and the Hudson Motor Car Company constructed the facility in 1941 to manufacture various artillery and shells. The facility was subsequently owned by Westinghouse and Ford Motor Company before it was purchased by the Chevrolet Motor Division of General Motors in 1961. From 1961 to 1974, the facility was used to manufacture automotive parts and artillery shells. From 1974 to July 1980, Chevrolet continued its automotive manufacturing operations. The Hydra-Matic division of General Motors began operations in 1980 and continues to produce transmissions and various other automotive parts.
It was the task of North American Dismantling to finally clear out all the old and redundant systems that had been collected over the years, including electrical, mechanical, fire protection, heating and ventilating, and security systems. No as-built drawings were available to assist North American Dismantling in this endeavor. Several hundreds of hours were spent identifying and labeling the systems to remain and those to be removed.
All abandoned pipes, conduits, and wires were removed from the inside and below the roof truss of the buildings. Conveyors, mezzanines, catwalks, and their supports no longer used were removed completely. All equipment support brackets were removed. Steel brackets and clamps for pipes and conduits were removed from roof trusses and building columns in the identified dismantling area. North
American Dismantling removed all old equipment structural members, u-bolts, and hangers connected to roof trusses in all areas.
Additionally, North American Dismantling removed 45,000 square feet of wood block flooring, 56,000 sf of concrete pavers, and 244,750 sf of non-monolithic concrete (including topcoats, concrete pads, concrete curbs, and equipment foundations). The wood block flooring and brick pavers were removed and disposed of as regulated materials, and the areas below were scarified to receive new concrete topping.
North American Dismantling also removed several hundred feet of 48” round ductwork, which covered an area of approximately 200,000 sf from the existing roof.
North American Dismantling completed the asbestos abatement of pipes, heater units, and HVAC units located in the truss of the buildings.
North American Dismantling also completed the environmental cleaning of all pits, sumps, flooring, and trenches in all areas.
In addition to our original contract work, North American Dismantling was awarded the removal of approximately 12,000 sf of the existing oven from the roof area. The ovens were contaminated with non-friable ACM. In Addition, North American Dismantling received the proper 40 hr training needed to remove the ovens. The roof, roof panels, and side panels of the Elpo Oven were double-wrapped with 6-mil poly and disposed of as ACM. The remainder of the oven was removed as non-hazardous metal and debris. Because of the high flammability of the roof, North American Dismantling, in conjunction with the Plant Fire Marshall, purchased four plasma cutters and trained its employees to complete these operations.
Process Equipment Demolition Paint Shop Spray Booth and Ovens
Moraine, OH – This project consisted of the removal of approximately 50,000 sf of paint ovens and 10,000 sf of paint spray booths located on the second floor and grating level of the plant directly adjacent to the operating paint shop. There were several factors that made this a very complex and unique project. Aside from being located directly adjacent to the paint shop, the second floor and the grating level were built over the old roof (R-1 Level) of the existing assembly plant with an active assembly line located directly below the roof area. The use of water for fire protection had to be minimized and all openings in the R-1 level had to be protected to prevent any foreign mater from entering the assembly area. Also, active paint conveyors were located on the R-1 level directly below the demolition area which had to protected from the demolition operations.</p?
Absolutely no dust or foreign matter could come in contact with these systems. Another hurdle to overcome involved having no major access and egress to the demolition area until NADC designed and installed a series of structural steel bridges consisting of 60 tons of material connecting the demolition areas to a drop zone at the edge of the existing building. This operation required opening the existing building in five separate areas and installing a weather protection system to eliminate any elements from entering the plant. The construction of these bridges included airlifting structural members utilizing helicopters, which was completed on plant down time (Sundays and Holidays). North American Dismantling was also responsible for the design/build of $1,200,000.00 of the structural steel/grating and concrete utilized in filling all openings where the booths and ovens were removed, along with utility disconnects, rerouting and re-supporting and the relocation of existing process equipment. Additionally, during the course of its contract GM requested North American Dismantling remove an existing 240-foot long, 80-foot wide and 80-foot tall Automatic Retrieval System (Stacker Building). This structure was connected on two sides and was 30 foot taller then an existing building, which was to remain. This project was completed on schedule, with limited change orders and without interference to the plant’s existing assembly operations.
Contact us for more detailed information on your industrial strip out project.